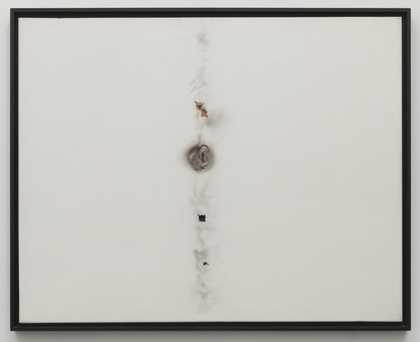
Fig.1
Henk Peeters
Burn Hole 1961
Plastic and wood
800 x 1010 mm
Tate T13407
© Estate of Henk Peeters
The twenty-first century would be unrecognisable if plastics did not exist: this ubiquitous modern material emblematises our everyday, consumer-driven culture, and can be found in all areas of life, including art. In this essay we look at the background to Henk Peeters’s choice of material for Burn Hole 1961 (Tate T13407; fig.1), how he may have made the picture’s distinctive holes, and the conservation challenges posed by the work’s material, once seen as long-lasting but now recognised as both potentially fragile and prone to deterioration.
Plastic is a name given to a variety of natural, synthetic and semi-synthetic materials, which can be moulded into a range of forms. As the term suggests, these materials exhibit ‘plastic behaviour’. The earliest plastics occurred naturally and their use can be dated back to prehistoric times. Horn, amber and tortoiseshell, to cite a few examples, are natural plastics that may be reshaped using heat. In the nineteenth century, scientists such as Alexander Parkes in Birmingham and Leo H. Baekeland in America created new plastics. These were based on natural materials, such as cellulose, derived from wood pulp, or casein, derived from milk products, which were chemically modified in the laboratory and used to create semi-synthetic plastics. One of the most notable was cellulose nitrate, crucial to the creation of the modern film industry and most commonly known as celluloid. Entirely synthetic polymers emerged onto the market in the mid-twentieth century, products of developments in chemistry driven forward by the challenges of the Second World War. Derived largely from petrochemicals, synthetic polymers were used to form new plastics such as polyvinyl chloride, polystyrene and polyethylene.
Much like metal alloys, plastics are composite materials made from two or more constituents with different chemical and physical properties. With plastics, however, the principal material is comprised of one or more organic polymer (a term derived from the Greek, polumerēs, meaning having many parts) combined with various additives, such as plasticisers, pigments or UV stabilisers, which endow the plastic with a number of desirable properties. Organic polymeric materials, however, will all degrade over time, whether natural or man-made, and tend to pose significant stabilisation problems due to their methods of production and the inclusion of additives.
The physical characteristics of polymers are based on their high molecular weights and their underlying crystalline and non-crystalline structures. Processes of deterioration, such as hydrolysis and thermal degradation, which alter the structure of these polymer chains, result in changes to the materials’ properties and stability. When considering the thermal properties of plastics it is common practice to group materials into two types: thermoplastics and thermosets. Thermoplastics are those where the material is softened by the application of heat and will become ridged on cooling. Further heating will reverse this process, softening the plastic and enabling it to be reshaped and moulded numerous times (this class of material is central to household recycling processes). By contrast, in thermoset plastics the polymer takes the form of a viscous fluid or powder that can be readily cast into a mould and is solidified through the addition of a catalyst. The catalyst causes a three-dimensional network of chemical bonds to occur throughout the material, rendering it a rigid solid which, on the application of heat, cannot be softened or manipulated further. As will be seen, the thermal properties of plastic are, of course, particularly relevant to Peeters’s pyrographies, which involved modifying materials with burn marks through the controlled application of heat.
At a time when avant-garde artists were interested in using distinctively modern materials, Peeters began to use plastic sheets to make pyrographies from 1959.1 He used a range of off-the-shelf materials, including polyurethane (PUR) foam and polyvinyl chloride (PVC) film. Analysis of a sample taken from the back of Burn Hole shows that the polymer film used by Peeters is a phthalate-plasticised PVC containing titanium white pigment. PVC is one of the most widely manufactured and used class of synthetic plastics. It was first developed in the 1920s but its popularity grew after the Second World War when its durable and flame-resistant nature was exploited for uses such as the insulation of electrical wire. It has also been used for sheeting, flooring, shoes and rainwear, toys, adhesives, and guttering and drain pipes, each having quite different characteristics and appearances created by the use of additives, notably stabilisers and plasticisers.
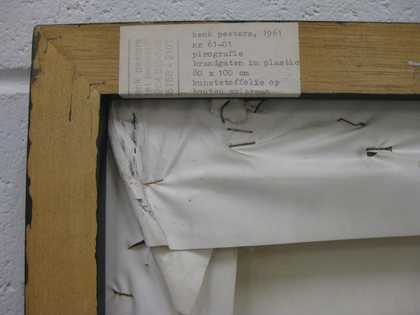
Fig.2
Rear view of Peeters’s Burn Hole showing the PVC film pulled and stapled over the wooden stretcher
Tate
© Estate of Henk Peeters
A thermoplastic material, PVC has the propensity to undergo deformation at raised temperatures under the application of force. By increasing the temperature of polyvinyl chloride, the non-crystalline, disordered regions of the polymer are provided with enough energy to move and rearrange. The temperature at which this rearrangement happens is termed the glass transition temperature and is the point at which a material moves from a glassy, rigid solid to a flexible, malleable solid. Raising a material above its glass transition temperature enables it to be readily manipulated into various forms, including extrusion as sheets that retain their form when they cool. With the inclusion of additives, such as plasticisers, the glass transition temperature and the temperature at which the material can be deformed are lowered, thus providing a plastic that is flexible at ambient temperatures.2 Employing differential scanning calorimetry, the sample from Burn Hole has been shown to have a glass transition temperature just below ambient temperatures, with the onset of the transition occurring at approximately -15°C.3 This quality meant that the polymer film Peeters used was soft and flexible at room temperature, making it easy for him to stretch the sheet taut over the work’s wooden frame (fig.2). The stapled folds of the film have a tactility that would not have been possible with a stiffer plastic.
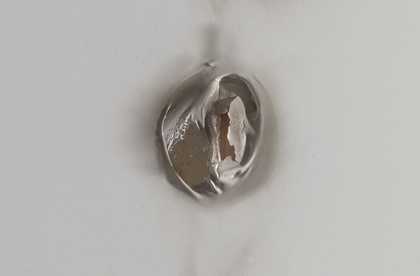
Fig.3
The central hole in Peeters’s Burn Hole photographed in raking light
Tate
© Estate of Henk Peeters
Analysis of the sample has also provided information on the melting temperature and temperature of decomposition. Between 100°C and 250°C the sample was seen to exhibit a series of endothermic responses, absorbing energy which led to the melting of various crystalline structures formed during the initial processing of the PVC film. Above 250°C the sample was shown to fully decompose. When PVC is exposed to heat, the polymer undergoes a number of chemical alterations resulting in the release of hydrogen chloride gas, a process called dehydrochlorination. The evolution of this gas poses risks to the environment and health, which is why PVC materials are not suitable for temperature-dependent recycling techniques. The result of this initial decomposition is a material that ranges in colour from yellow and orange to brown or black depending on the extent of decomposition. These temperature-dependent alterations account for the colour changes exhibited across the surface of Burn Hole. The large hole in the centre of the film is surrounded by undulations in the surface of the film and gradations of brown and black (fig.3), indicating that there were differences in temperature during the melting and scorching of these regions. The large central region exhibits a melting pattern characteristic of slow heating and distortion of the film owing to softening, suggesting that these effects were created using the heat generated by a candle. Although the internal temperature of a candle flame can reach temperatures between 900 and 1200°C, well above the point at which this PVC film would show complete combustion, the regions above a candle flame can produce temperatures sufficient to cause melting, discolouration and the formation of soot. At a vertical distance of 10 cm from the flame of a beeswax candle the air temperature is in the region of 100 to 150°C. Such temperatures would be sufficient to soften the PVC film and initiate dehydrochlorination and colour change. The presence of soot appearing across the work would also indicate the use of a candle, with deposits being formed on the surface of the PVC, due to the presence of solid particles of unburned carbon originating from the wax.
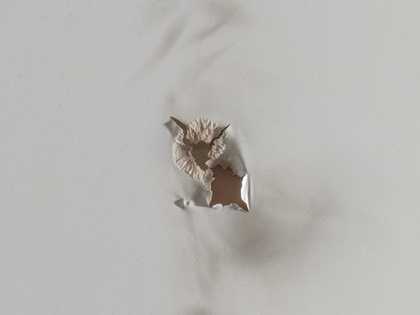
Fig.4
The uppermost hole in Peeters’s Burn Hole
Tate
© Estate of Henk Peeters
The other, smaller holes seen across the work exhibit quite different characteristics (fig.4). Showing a complete combustion of the polymer, they are spherical and reminiscent of cigarette burns. The temperature of a lit cigarette is in the region of 600°C, which quickly rises to temperatures approximating 950°C as air is drawn into the cigarette. These smaller, highly resolved burn holes could have been easily produced by placing a smouldering cigarette up against the surface of the polymer, taking the temperature well above 250°C, the temperature of full decomposition.
It is interesting to note that Peeters often used mass-produced materials in his art such as nylon and PVC, which he bought from inexpensive shops. He liked the clean and modern appearance these materials offered, stating that ‘with my work I have always wanted it to look just as fresh as if it was in the HEMA’, referring to a Dutch high street general goods shop.4 Such statements are particularly interesting for conservators who must decide on a best practice conservation strategy for artworks. Many artists working with plastics believed that the new material was indestructible or at least long-lasting, but many early plastics deteriorated relatively soon after production.
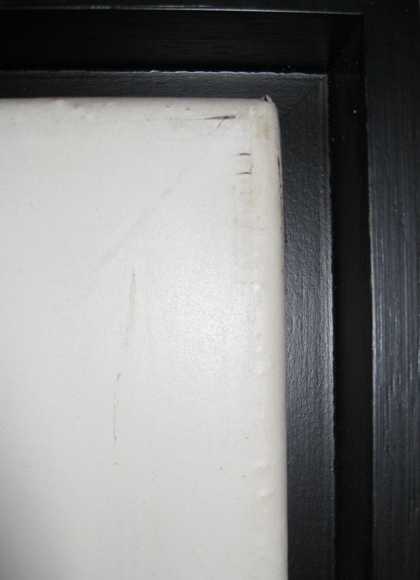
Fig.5
The top right corner of Peeters’s Burn Hole, showing deterioration of the material
Tate
© Estate of Henk Peeters
Despite the relative instability of plasticised PVC, Peeters’s Burn Hole is currently in a relatively ‘good’ condition in that it appears to have retained its colour and shape, with minimal losses to the surface. The ageing of plasticised PVC is dependent on the conditions of storage and display, composition of the plastic and the degree of plasticisation. The work is maintained in optimum environmental conditions, which helps to delay deterioration often caused by raised temperatures, light or high humidity. The presence of optical brighteners, such as the titanium dioxide pigment, also provides resistance to light degradation and help counter colour change caused by a high degree of plasticisation. However, there is evidence of the initiation of deterioration where the material is cracking at the edges wrapped around the wooden frame (fig.5). Polyvinyl chloride often experiences migration of plasticisers, which is seen as an oily exudate on the surface of the material or the formation of crystals. The loss of such material through the polymer matrix causes shrinkage and embrittlement, which in the case of this picture may have been exacerbated by the tensile stresses caused by stretching the film across the work’s wooden frame.
Not unexpectedly, the most fragile sections of the work are those that have been burned and are now highly sensitive to air flow caused by movement and localised stresses. For this reason, a bespoke conservation backboard was fitted to the work in 2011 to help prevent movement of the film during handling and transport, and care is taken to ensure stable display and storage environments.5
It is very difficult to predict the life span of polymer-based artworks as they can be stable for many years before a rapid onset of deterioration causes irreversible changes in condition. An option used occasionally and when ethically appropriate is to create an archival replica for the purposes of study and display, employing the same or more stable materials. Peeters himself was open to the replication of some of his works and, conceivably at least, this could be an option if Burn Hole were to deteriorate beyond what might be deemed an acceptable condition.6 However, when he attempted to replicate 59–18 1959, a work made from polymer polyurethane (PUR) foam, he discovered that ‘present-day PUR foam contains fire retardants and it burns “not so nice” as in the old real PUR foam’.7
When undertaking treatments of modern and contemporary artworks conservators strive to respect the artist’s intention and retain the authenticity of the work, an approach that becomes difficult when the original materials cease to be manufactured and new alternatives are not quite right. Peeters originally intended to allow anyone to make new versions of his works, but his known dislike for the ‘not so nice’ plastics produced later highlights the limitations of this option.8 Although the plastic sheets Peeters used in his pyrographies originally symbolised modernity, the unstoppable eventual deterioration of these works, involving discolouration and loss of plasticity, will inevitably force us to accept the material’s ageing processes and changing appearance.