In addition to standard analogue production routes, I have also explored the production of slide duplicates using digital intermediates which were created using light valve technology (LVT) film recorders onto sheet film, cathode ray tube (CRT) film recorders printing onto in-camera slide stock and motion picture reversal stock, laser film recorders printing onto microfilm and inter-negative 35 mm motion picture stock to produce slide duplicates as film prints. The results are summarised in the chart below:
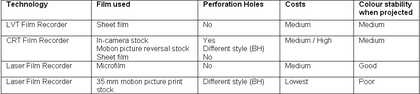
Summary of alternative production routes
Light valve technology film recorders
Light valve technology (LVT) film recorders, such as Lightjet 5000 and Durst Rhino II, are able to produce very accurate duplicates. As with all of these technologies, these film recorders depend upon the expertise of those able to maintain and calibrate them; an expert knowledge that is increasingly rare. The recorders that are still in service have been purchased second-hand long after commercial support has come to an end. I have witnessed problems in the sharpness of the image caused by the misalignment of the light beam, this is particularly visible when the sheet film chosen lies at the limits of the device.
The potential disadvantage of this method for the purposes of duplicating slides is that sheet film does not have perforation holes; hence the exact registration between the slide image and the perforation holes is lost. This is a particular problem for slide works that require exact positioning of the slide inside the mount for their playback – for example, in a work which incorporates dissolves and cross-fading where images are overlaid on each other using a number of synchronised projectors. Cutting out the individual 35 mm slides from a sheet of film can become laborious. However, there is also an advantage ecomically as one 5 x 7 inch sheet can produce up to fifteen 35 mm slide exposures and one 8 x 10 inch sheet thirty-five 35 mm single exposures. Doug Munson at Albumen Works has achieved great results with this method and is the only professional photography conservation laboratory that, by using this method, offers in-house slide duplication.
Cathode ray tube film recorders
Cathode ray tube (CRT) film recorders, such as the Agfa PCR II Plus, support a larger variety of stocks owing to the variety of interchangeable fittings which are called camera movements. These include 35 mm, 70 mm and medium format film of different length rolls, as well as sheet film in different sizes. CRT recorders are an older technology than LVT, however if properly maintained and calibrated they can achieve equally good results. The main advantage of CRT recorders for slide duplication is that 35 mm perforated film can be used.
Despite earlier discontinuation notices in July 2012, the remaining slide stocks that are still available are FUJICHROME VELVIA 50 / 100 / 100F (35 mm, 120, 4 x 5, 8 x 10), FUJICHROME PROVIA 100F (35 mm, 120, 4 x 5, 8 x 10) and FUJICHROME PROVIA 400X (35 mm, 120). Especially without FUJICHROME VELVIA 100F the future use of film recorders for slide duplication will be jeopardised. In the tests that Tate conducted with Activity slide laboratory, we also explored using a motion picture reversal stock in a CRT recorder in order to see if Kodak E100D stock, which at the time of writing is still being made, could be used as an alternative to the discontinued slide stock Kodak E100G. In evaluating the results, the similarities between the slide stock Kodak E100G and its motion picture equivalent Kodak E100D was striking. The results of these tests showed that the emulsion of both stocks is very similar and that Kodak E100D could be used instead of slide stock. However, motion picture stocks have Bell & Howell (BH) perforation holes which are a different shape to photographic stocks which have Kodak Standard (KS) perforations. In order to transport films with BH perforations, a camera movement is needed that supports this type of hole.
Laser film recorders
At the time of writing, laser film recorders and microfilm continue to be commercially supported technologies and are continuing to be developed, for example the Arche laser recording system for colour microfilm that was developed by the Fraunhofer Institute for Physical Measurement Techniques IPM in Freiburg, Germany.
Ilfochrome Micrographic is a high resolution direct positive colour film whose processing is based on silver-dye bleach technology (P-5 process). Though in principle microfilm should not be capable of getting even close to the dynamic range of slide film, tests that I carried out at Mikrosave in Switzerland showed surprisingly good results. One significant advantage of microfilm is that it is designed to have outstanding ageing properties. To test the dye fading properties of microfilm inside a slide projector, I projected two slides for three continuous days, exposing only part of the image to light. One slide was made using Kodak Edupe and the other was made using Ilfochrome Micrographic Type P. The results were evaluated by eye and the microfilm appeared to be approximately five times more light stable than slide duplication film. Microfilm is produced as sheet film and roll film but does not have perforation holes.
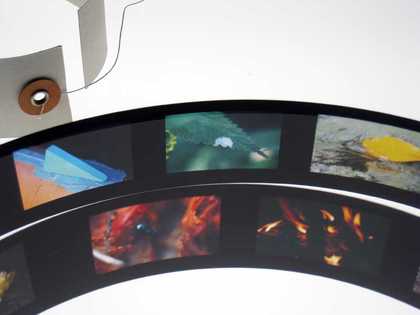
Strips of microfilm without perforation holes
Inter-negative film
The final alternative production route tested is directly based on that of motion picture print films. Here the tonal values of the digital file need to be reversed to produce an inter-negative from which slides can be made. This method is not new and has been used as a low-cost means to produce duplicates since the 1960s. However, in 1993 Henry Wilhelm stated that this method of duplication was considered low quality owing to the low resolution of print stock, which matters less in moving image (because each frame is only projected for one twenty-fifth of a second), and also to the colour instability of certain print stocks1 . Given that film production methods and the quality of stock has improved since the tests referenced by Wilhelm, this method of producing slide duplicates has recently been re-examined by Maurice Schechter of DuArt Media lab (discussed at TechFocus II: Caring for Film and Slide Art, April 20122 ) and also at the National Gallery of Canada where Ainsley Walton has investigated this as an archiving strategy for slide-based artworks as part of the DOCAM project.
All four of these production methods require the original 35 mm slide to be digitised. This means that initial costs are significantly higher when compared to the analogue production methods. However, once digitisation has been carried out, the long-term costs of producing slides are comparable to analogue duplication.
Resources
- Download the technical data for the Laser recording system for colour microfilm (PDF, 513 KB)
- Download the technical data for the Kodak Professional EKTACHROME Films E100G and E100GX (PDF, 106Kb)
- Download the technical data for the Kodak EKTACHROME 100D Colour Reversal Film (PDF, 103 KB)
- Download the technical data for the Ilfochrome Micrographic colour film (PDF, 159 KB)